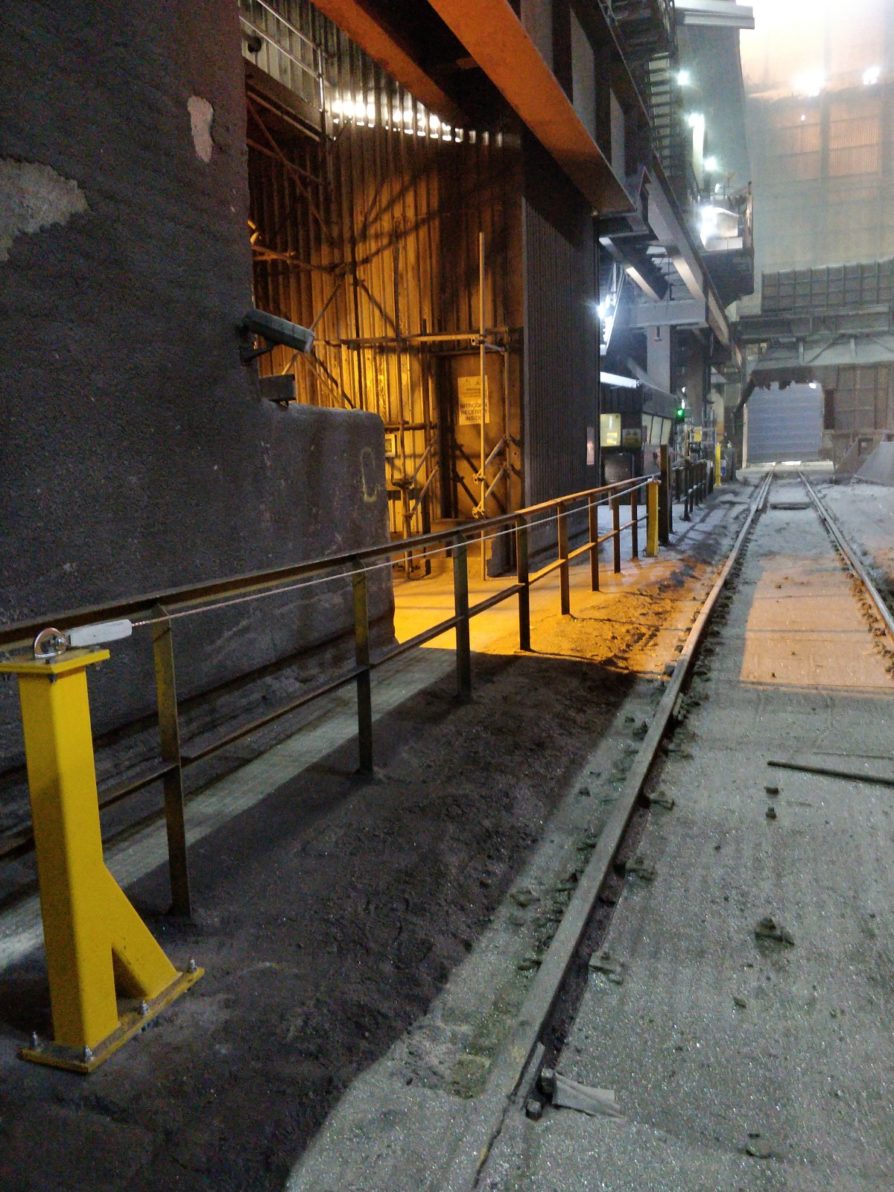)
RSS installs fall restraint systems at steel facility
Rope and Sling Specialists Ltd. (RSS) has designed, fabricated and installed four bespoke fall restraint systems at Tata Steel, Port Talbot, Wales.
The solution consists of eight bespoke fall restraint posts, designed and fabricated by Gemmak Engineering, part of the RSS Group, and four MSA Latchways fall protection systems that, in combination with full body harnesses and lanyards, allow safe access to a railway track located near an open pit.
A torpedo car is employed on a railroad to transport molten metal from the BOS (basic oxygen steelmaking) plant and take it around the facility as part of the primary steelmaking process. The end user is required to perform planned inspection and maintenance on a rail that involves working at ground level, located next to an open pit with a risk of a fall.
The systems are either 12m or 14m in length, fixed to 1.3m high posts; they are fixed together using M16 bolts, nuts and washers. Atop the posts are MSA Latchways heavy-duty D-rings, while all floor fixings are M16 x 200mm Hilti resin anchor rods. The rope, which spans varying gaps between the two posts in each system, is marine-grade stainless steel, 316 8mm, in 7×7 construction. All structural steel work complies with BS EN 1090 (marking for structural steel and aluminium fabricators) execution class II and applicable working at height regulations.
Matthew Rogers, engineering services director at RSS, says, “The end users arrive at the system already wearing a full-body harness with set-length lanyards that they connect onto the line using the provided PPE (personal protective equipment). The length of the lanyard means that they can carry out their periodic inspection work in complete restraint, removing the original fall risk. The whole solution was fabricated, using the latest design, cutting and welding technology.”
This was RSS’s first installation since being named an MSA Latchways approved installer. Rogers explained that the project timeline, including manufacture, spanned ten days from the receipt of the order to installation and commissioning onsite. RSS had to add extensions to certain posts in order for the systems to accommodate obstacles in the facility.
The application served as another example of the company’s expanded engineering capability, having fully integrated the Gemmak Engineering business, located near to de facto headquarters in South Wales, that was acquired 18 months ago. The facility will be the company’s eighth in the UK upon opening of its latest lifting and rigging depot next year.
Rogers says, “Engineering services is doing extremely well nationally, with eight new staff employed since May 2020; we have two new starters this month [November]. We do have more capacity and are currently working on a ten day lead time, as this case study demonstrated, depending on the complexity of the project and receipt of order.”