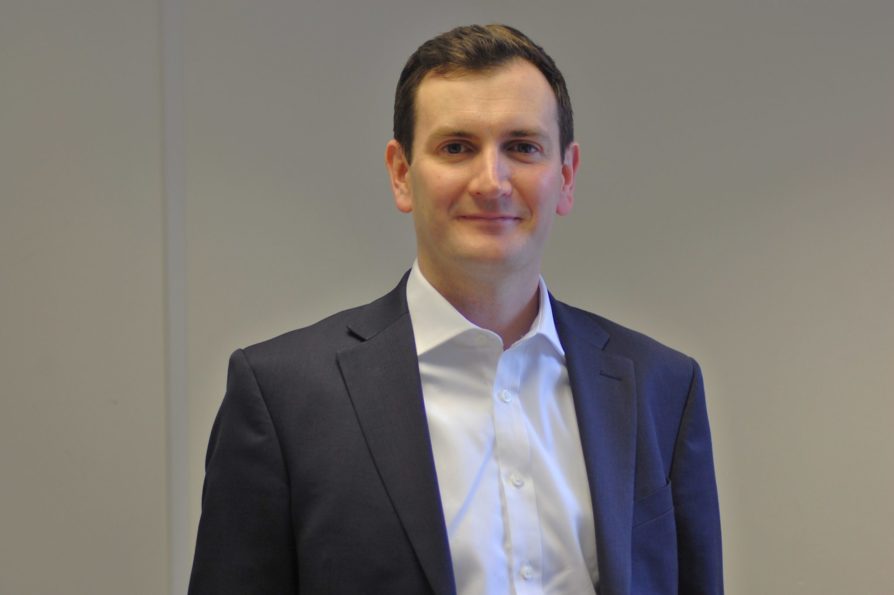)
What’s behind the audit that earns a LEEA badge?
Ross Moloney, CEO at the Lifting Equipment Engineers Association (LEEA), gives an impression of the rigorous LEEA audit process that ensures the Association badge upholds its ‘gold standard’ reputation.
In my previous column I commented on the need for companies to ‘trust in experts’. Carrying a LEEA badge is good sign to easily identify an expert because it shows that the provider is a member of the Lifting Equipment Engineers Association. To become an Association member, the provider will have undergone a rigorous auditing process to uphold LEEA’s ‘gold standard’ and provide customers with the assurance of excellence and compliance to standards and legislation. LEEA’s audit process provides reassurance to the many tens of thousands of ‘duty holders’ – often with little personal knowledge of the subject – who bear responsibility for the safe design, maintenance and operation of the lifting equipment and services their firm buys, hires or contracts in. Using audited LEEA members gives duty holders a guarantee that those aspects of their responsibilities will be faithfully, professionally and lawfully discharged.
A brief run through the key areas we look at when conducting a LEEA audit on a company, without going through an exhaustive list, will give end users an idea of the comprehensive adherence to quality represented by the LEEA logo.
Does the organisation structure of the member company identify key personnel and are they trained in the operation’s scope of work? Members are required to demonstrate that they maintain training records for their employees and that they are practically and theoretically competent. If using a subcontractor – how are its competencies verified? Does the member have the correct reference material in place – either on hand or available through its technical department? Is this information being shared with its employees?
Modern legislation places an emphasis on manufacturer’s information and instructions for safe use – does the member own this information? With many products covered by national, European or international standards, members will need to refer to these documents and must hold, or have ready access to, those standards covering the normal scope of work.
A member should also hold copies of current legislation applicable to its company, together with approved codes of practice and guidance documents. What test and verification equipment – such as test beds, test weights, load links, verniers, etc – are held? How are these items verified and does the member have a current in-date calibration certificate to show that the equipment is being calibrated to the correct standard?
Being a legal document, does the member’s Report of Thorough Examination comply, as it must, by containing all the relevant information? If the member is manufacturing or assembling lifting equipment, does its Certificate of Conformance contain all the information required?
Who owns or has the ability to compile a member company’s technical file before its equipment is placed on the market or produced upon request? We check that the technical file contains all the relevant information: reference to standards, certificates of tests, design calculations and drawings, certificates of conformity and incorporation, manufacturers’ instructions, etc.
Is the member receiving and issuing the correct documentation for factored goods – ie, goods bought in to sell on? LEEA’s stance continues to be that members should issue the original Certificate of Conformance along with instructions for safe use when selling on.
Does the member hire equipment out? If so, it must be able to show its documentation trail, which should begin at goods-in and go all the way through to goods-out.
Moving on to examination facilities, are they clean and tidy? Is there suitable work area segregation to avoid confusion in identifying items? Is the quarantine area marked up, clean and is it being used correctly?
As this brief outline demonstrates, the audit does not just provide a snapshot of compliance and competence at a moment in time. In fact, it provides a development mechanism that ensures that each and every LEEA member rapidly achieves, and maintains, the highest international standards. So, a LEEA audit is not only a valuable feature of LEEA membership, it is a badge of excellence for end users of lifting gear.