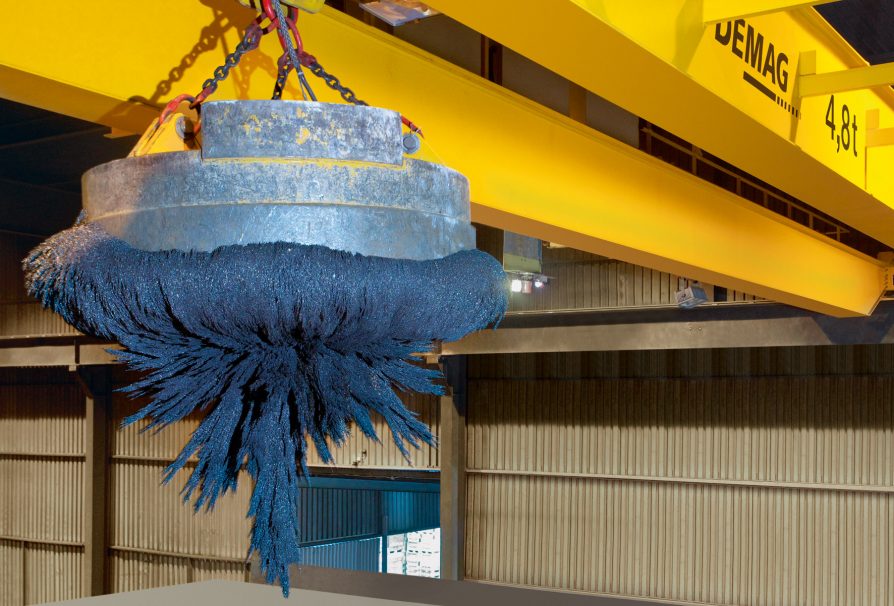)
Demag Process Crane for Swedish Iron Foundry
Swedish iron foundry Arvika Gjuteri AB has commissioned a new ZKKW double-girder process crane with an integrated weighing and position measuring system.
With the investment in modern crane technology, the manufacturer, with a long tradition of producing castings for commercial and off-road vehicles, will increase handling rates for scrap in line with its increased production capacities.
“In order to meet the growing requirements of our customers, speed and precision are the decisive factors when collecting the material,” said Anders Nilsson, project manager at Arvika.
The process crane has replaced an older crane model and is responsible for collection of scrap material, also known as charge make-up, and its transfer to the induction smelting furnace.
With the old crane, employees had to work 24 hours a day in the scrap yard and melting shop. Now the new crane can handle the same weight of scrap in less than two shifts.
The crane, which works five days a week in two-shift operations, first takes the material with the largest quantity from a box and, at the same time, determines the weight via calibrated crane scales integrated in the open winch crab. On the basis of this data, the quantities for further material are determined, transmitted to the cab by radio and displayed.
As soon as the desired final formulation is complete, the mixture is then tipped onto a heap of scrap from where it is conveyed to the smelting furnace. The more precisely the respective mixture is produced by the crane, the fewer high-cost alloys are required.
The Demag ZKKW double-girder crane has a span dimension of 22.65m and travels on a 40-metre-long crane runway. It is equipped with a multi-purpose MPW open winch, characterised by its compact and maintenance-friendly design. The load is picked up using a round magnet connected to the hoist by a 4/2 reeving arrangement.