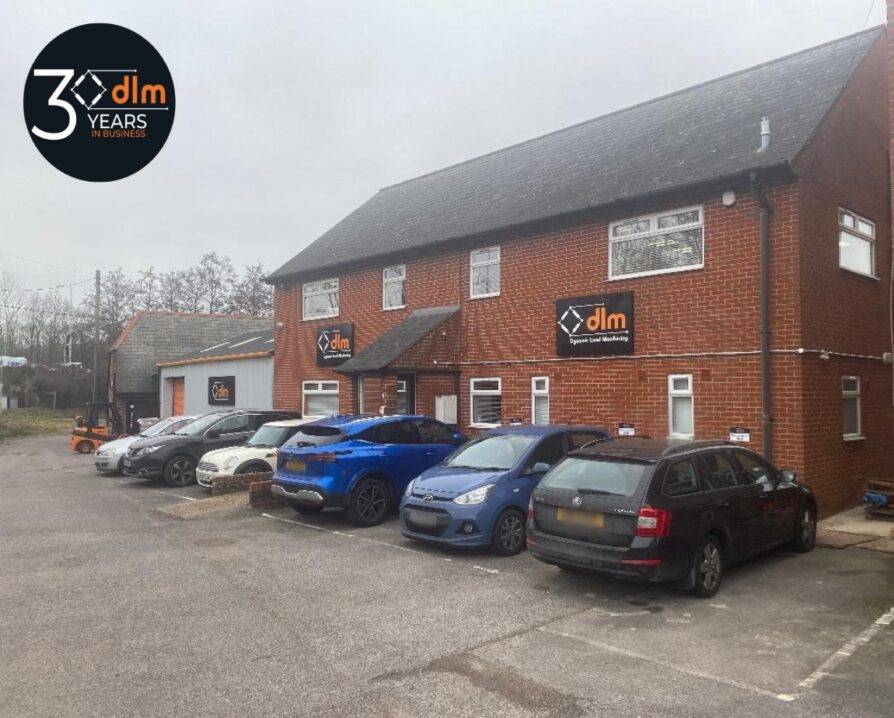)
DLM celebrates 30 years
Dynamic Load Monitoring (UK) Ltd. (DLM), of Southampton, UK is celebrating 30 years
The manufacturer of force measurement equipment will stage a series of events, including a staff away day, culminating in a celebration in the summer, which chimes with Martin Halford, managing director, completing 14 years of ownership.
Today, DLM provides running line monitors (RLMs), saddleback monitors (used in pre-lay grapnel run and route clearance operations to measure line tension), load pins, and load cells that capture data as tension is applied to lifting and marine equipment. Turnover has grown almost 10 times since 2009, when Halford and his father, Jeff, acquired a company based in a converted barn, where a state-of-the-art, 8000sqft facility forms headquarters today. It employs 25 members of staff and has a facility in Singapore.
Halford said, “We bought the business on 1 October 2009, and I started the following month. My father was working in the offshore industry and joined me five years later, before retiring last year. I had no idea how to buy a business and didn’t really think it was possible, but that’s history now.”
Halford first walked through the DLM – that has always been the company name – door on work experience as a 15 year old. He continued to visit during holidays, while studying electronic engineering at university. He started work as a technical sales engineer elsewhere but kept in touch with DLM’s previous owners and was aware of their plans to eventually sell-up and retire.
The company’s journey can be charted through various product innovations. It started supplying subsea load pins to the offshore cable laying industry, while tensile and compressive load cells were in demand from local and national lifting companies. Growth overseas dovetailed with expansion of calibration services, as DLM expanded into electronics over time. All these products and expertise remain central to the company’s offering today.
Halford said: “We still work in the same industries but have expanded and improved our product offerings and scope of our supply internationally. We have always tried to maintain the mentality that customer service is our priority, and our ethos is built on finding a way to solve project challenges. This in turn leads to product innovations, such as our de-trenching and other grapnels. As we’ve expanded, there’s been a requirement to reinforce our product provision with [ISO, ATEX, and other] accreditations.”
DLM has now purchased its facilities, with set-up of a marine sales division (2015) and moving into new offices (2017) standing out as major milestones. Investment has continued in the hire fleet, as demand grows for short- and mid-term use of products such as its RLMs. Halford also pointed to development of the TW-3.0 handheld, which is a wholly owned DLM product; expansion of computer-aided design and engineering technology and personnel; and increased presence in subsea and renewables sectors. In fact, subsea load pins are a best-seller.
He added: “We are constantly innovating and looking at how our products can be better. We want to totally digitise the company and all its processes, and in the next three years we want to go paperless. We also want to position ourselves as the prominent load cell manufacturer in the lifting industry and continue to be known for offering custom solutions to clients’ requirements. Longer term, we aim to be the key equipment supplier to the offshore cable lay industry and be able to offer a complete package to clients ahead of projects.
“We will likely also need to expand both domestically and internationally, with nearly half of our current business already being generated overseas.”