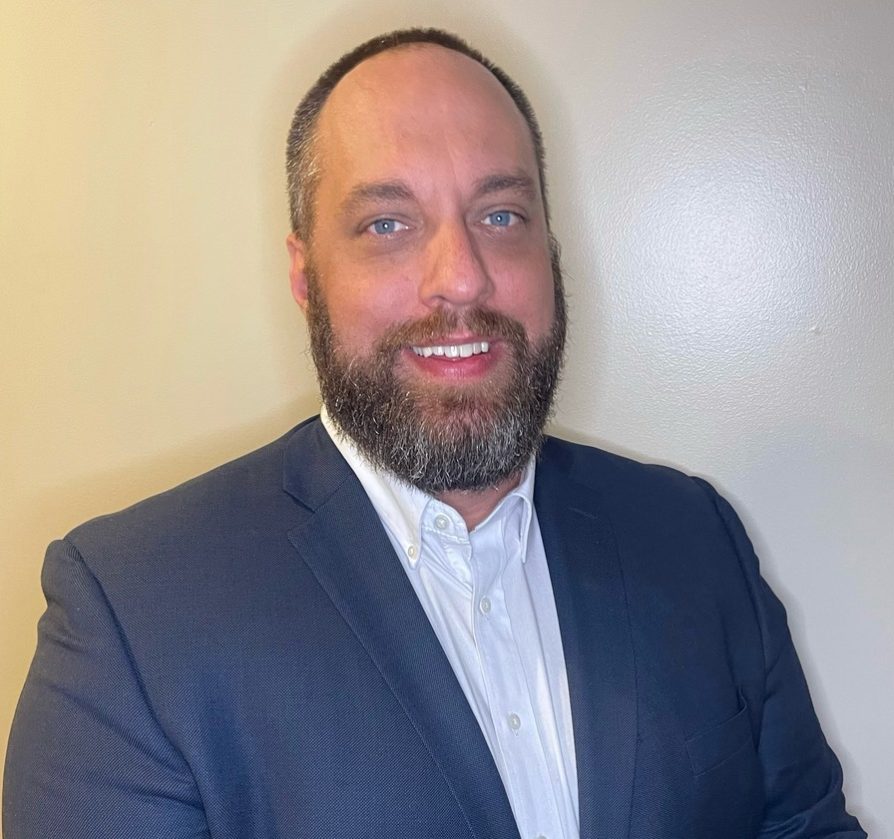)
O&M Energy
Operations and maintenance programming seems to be more important in some markets than others, which is exposed when implementing cross-industry strategy, says Joel Cox.
As I spend time with stakeholders in various markets, I’m reminded of the constant need to share knowledge that drives continued improvement of industry best practices.
At the time of writing, we’re on the cusp of American Clean Power’s (ACP) Operations, Maintenance and Safety Conference, which takes place in Orlando in early March. It is, inescapably, the place where industry leaders, experts and external stakeholders meet to tackle subject matter such as health and safety; operations and maintenance; and quality assurance, as we prepare for what organisers call, ‘an expansive future of the clean energy workforce’.
You’ll see operations and maintenance – more typically referred to as O&M – as a tagline to much activity in the wind energy and wider renewables sector, whereas it remains somewhat neglected elsewhere around electric overhead travelling (EOT) cranes and hoists. I’d go as far as to say that only in the nuclear sector, is crane O&M sufficient. It is remarkable, given the broad range of topics that fall into either the operation or maintenance brackets – or both – and the proximity of such lifting equipment to people and machinery – or lives and millions of dollars.
Regardless of the definition you use, O&M encompasses the functions, duties and labour related to the daily operations and repairs of equipment. It covers replacement of parts and components (brakes or otherwise) and all activities needed to prolong the lifecycle of an asset so that it provides safe service. People split hairs over certain descriptions but that’s basically it; if we don’t operate and maintain properly, equipment will fail, and accidents will happen.
As I’ve written before, EOT cranes can be up to 450USt or more in capacity. Imagine therefore the catastrophic scene when, say, a gear shaft should fracture, and a load is dropped. The damage to property and inevitable injury, or worse, to personnel is incalculable. It could even lead to the closure of a facility. It is not about highlighting the lack of brake maintenance in many applications, but we can look at O&M oversights much more broadly than that.
Even where an O&M programme does exist, it often isn’t based on duty cycles and wider safety strategy. Duty cycle is as important as capacity in cranes. Think about two identical 15USt capacity cranes: one lifts 12USt once a month, very slowly, only a short distance; the other lifts 12USt a hundred times a day, transports it the length of a factory, lowers it and returns to the start, where another load is already waiting to be rigged. It should be clear that these two applications have different duty ratings and O&M should be tailored accordingly.
You can guess one of the challenges, though: the higher the crane capacity and duty cycle, the more important O&M becomes but the less time there is for it and the more expensive it is to complete. I’ve seen steel and process cranes that are in almost constant use but because they’re operating in line with demand today, there is little acceptance that downtime is required to make sure they can perform tomorrow. Accessibility is a barrier to entry, literally, in this marketplace too.
It is also about connectivity between different safety procedures. One of the problems is that people tend to home in too narrowly on certain subjects, which results in them becoming universes in their own right; we lose the perspective of their place in the wider world. You might think ACP’s conference addresses rather broad subject matter, but operations, maintenance, and safety are a good mix. We can’t operate or maintain or be safe, can we? The same can be said when we’re looking to implement cross-industry strategy at companies that provide the same type of solutions to many different applications.
High time to change
Cranes by their very nature are often at height. Why then, is scheduled maintenance, access, egress, height safety, and rescue (see October 2022 edition), given more attention in one industry than another? Equipment is indiscriminate, remember, so O&M must have equal importance from one sector to the next. Believe me, it is more convenient to gain access to a crane during a maintenance outage than it is to scramble a team in an equipment or personnel emergency. Surely, we should be beyond preaching that by now.
My company, like many others, has a requirement to work in multiple end-user markets on any given day, even if my role is more wind-focussed these days. If it is important to us to share knowledge in-house that drives continued improvement of industry best practices, then each of these sectors must collaborate or match each other’s commitment to things like O&M.
Sometimes when I’m on a wind farm, I’m reminded of my time looking up at EOT cranes in the nuclear sector; we used to call it the ‘nuclear hot zone’. But every industry has its pressure – and breaking – point.