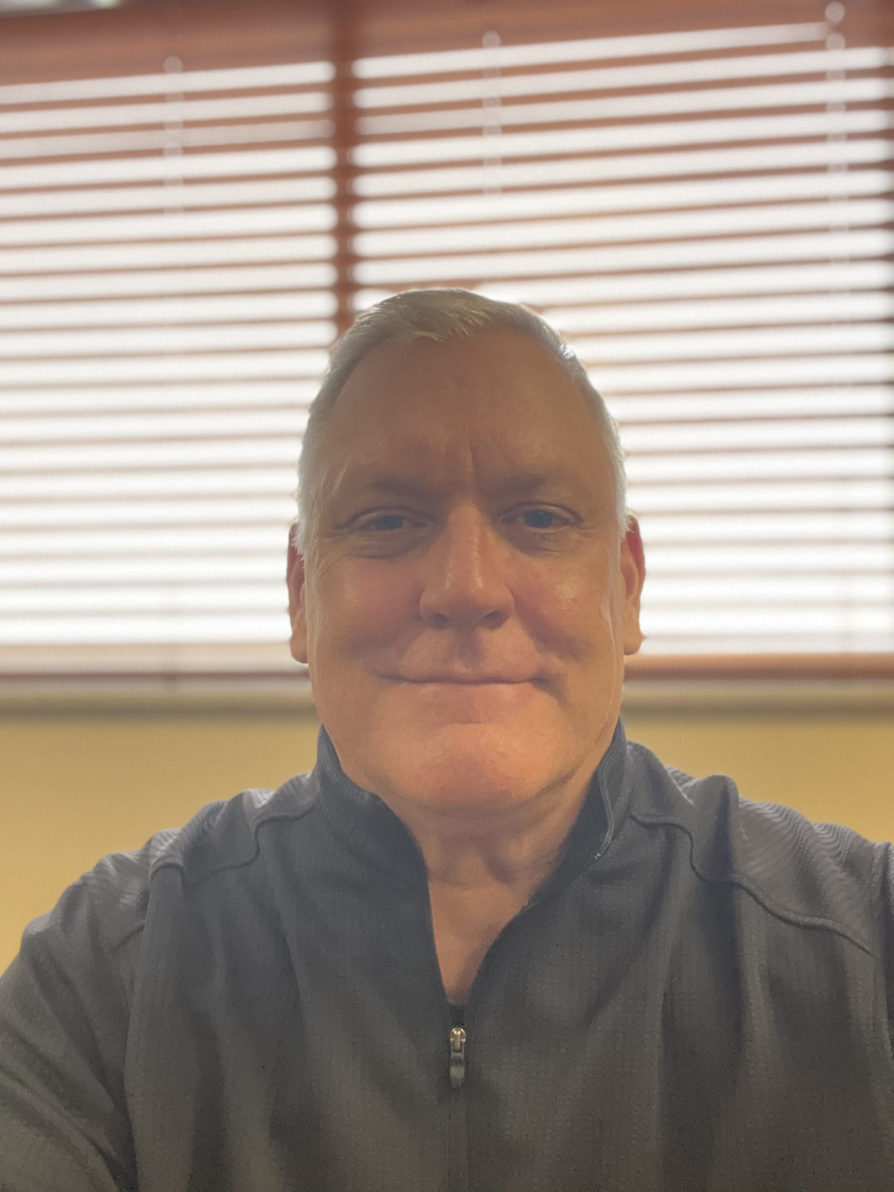)
The cut of one’s jib
As we continue to innovate as an industry, we can’t forget to present only the right tool for the job at hand, says Steve Napieralski, president at Oz Lifting.
The good news is that, as the lifting industry has innovated, supply chain representatives and end users have realised that such ingenuity leads to productivity and safety gains. There was a time where most people in the industry were late adopters when it came to new product innovations. However, over time, it was accepted that material handling applications vary greatly and what might be suitable for a 1100lb (500kg) lift in a warehouse might not be appropriate for a 1100lb (500kg) lift at a wastewater facility.
That doesn’t mean our work is done, though. As new professionals join the industry and we innovate at a faster pace than ever before, we must continue to promote the sharing of information for continued improvement of industry best practices. This education must still centre on choosing the right tool or product for the work at hand. While innovation means there is almost certainly a piece of equipment that’s perfect for the application, the breadth of manufacturer’s catalogues means that there is often an abundance of choice. This can lead to confusion, especially for the newcomer.
The great debate
The jib crane versus davit crane debate is a good example.
There’s no right, wrong, better, or worse product per se, but there is absolutely a right, wrong, better, or worse product to use in each instance. I’ll be honest, I have been involved with davit cranes for over 30 years, having first seen them in the wastewater industry, where they were used for pulling submersible pumps. However, I now often suggest a jib crane as the better solution in certain cases, especially where there is a need for a permanent lifting solution.
Let’s look closer at the differences between the two types of cranes:
A jib crane has an I-beam as the means of lifting a load and requires a trolley and hoist. These can be either manual or powered. A davit crane, meanwhile, uses a winch and cable to lift the load and is typically used in applications where they can move the crane from base to base. Most jib cranes require a cement pad to mount to whereas a davit can be mounted to a steel plate, concrete base or even be installed in the back of truck (we’ll talk more about bases later).
It’s also true that most jibs are made of steel, and davits can be made from steel, aluminium, or composite materials. Jib cranes offer a wider range of capacities, reach and height options; most manufacturing facilities use them for their material handling needs. As a result, you’ll see more jib cranes in some settings and more davit cranes in others. Hotbeds of davit crane activity include the already mentioned wastewater industry and property management, for example.
It was innovation that led to my business’s adoption of davit cranes and, while we offer steel and aluminium options, we also manufacture two composite cranes. As most readers know, a composite material is one that is made from two (or more) materials that have different chemical or physical properties but combine to create a material with properties unlike the individual elements. Practically, this means that cranes can be lighter, stronger, and less vulnerable to the elements.
One of our composite davits is made from pultruded fibreglass, which is what most ladders you’ve climbed are made from. This crane weighs roughly 80lb (approx 36kg) and can lift 1200lb (approx 544kg). Our second composite crane is made from carbon fibre, which is as good as it gets in the composite industry. Several high-performance sports cars are made from this material because it is strong and lightweight. The Boeing 787 Dreamliner is also made from it. Our Compozite Elite carbon fibre davit crane weighs just 37lb (approx. 17kg) and can lift 1200lb (approx. 544kg). Users also like that they can be moved from base to base. If a user wants to telescope the load in and out, our Tele Pro series is the better option.
Do you see how each product is suitable for different applications?
Base level
The importance of choosing the right product for the job at hand can also be demonstrated by davit crane bases and the options available. Without a base – or with the wrong one – a davit crane is not usable. There are typically three choices available.
- Pedestal
The pedestal base is commonly used on rooftops, where davit cranes might be utilised for maintenance or bolted to the floor in a facility. Users just mount the base where they need to make a lift and move the crane around.
- Socket
Socket bases are used mainly in the back of trucks or used in an area where the installer will pour cement around the base to keep the surface area flat and offer high mounting strength.
- Wall-mount
The wall-mount base allows a davit crane to be attached to the wall of a facility to save floorspace, perhaps on a production line or at a workstation. Each base comes with a mounting template.
In all cases, it is important to check the capacity of the mount and its compatibility with the crane/s selected. One wall-mount will not work for all davit cranes.
The industry isn’t done innovating yet, so end users can expect to see more products brought to market. Provided this innovation is driven by safety and productivity at the point of use, I’m all for it. As capacities increase and new technologies address certain application and material handling requirements, the onus is on all levels of a supply chain not to try to fit square pegs into round holes. Our ongoing progression as an industry depends on it.