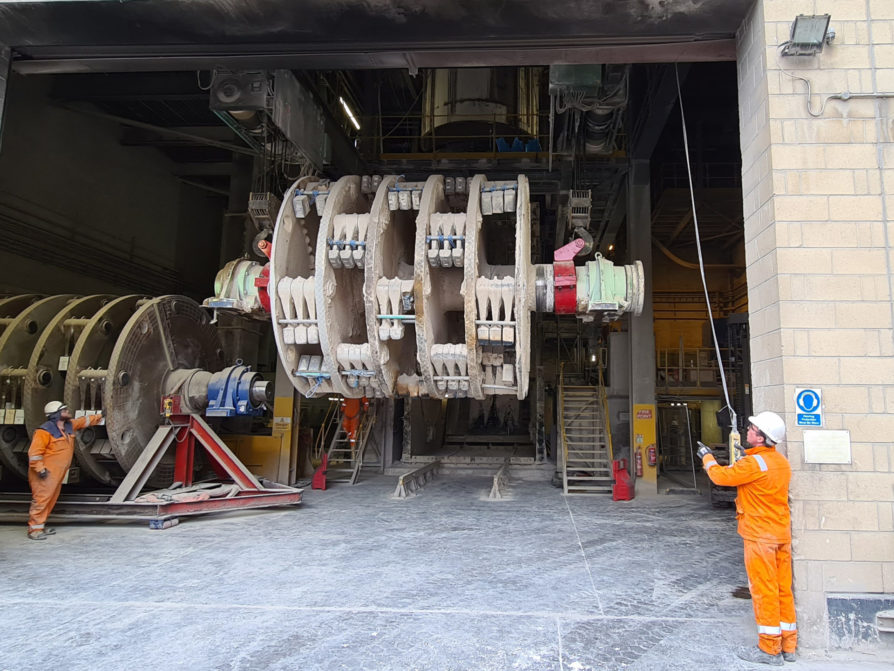)
Cementing the benefits of specialist services
The varied and specialist services available from Hoist & Winch Ltd have benefitted a cement industry customer that was looking to replace a large rotor used in its production process.
Thanks to the design, manufacturing, test, certification and installation services offered by Hoist & Winch, a cement works was able to avoid the long lead times associated with buying original OEM equipment, and successfully complete a highly complex and challenging lifting operation.
In essence, the objective was to lift and replace a large rotor fitted with pivot-mounted hammers that break down the media as part of the cement manufacturing process. Located at the base of a very large production enclosure, a pair of bearing journals provides support for each end of the rotor. Hoist & Winch had to design and arrange manufacture of equipment that would help to lift the worn and replacement rotors in and out of position in a precise manner without damaging any adjacent equipment, including the main drive motor and gearbox.
The cement works last performed this particular maintenance lift to replace a worn rotor in 2010 using a pair of lifting lugs that had since been disposed of. New replacement lugs were only available from the original supplier of the cement production process equipment on a very long lead time, which did not meet the requirements of the customer’s programme.
With a total design weight of 80t, rotor lifting was courtesy of a pair of tandem-controlled 41t SWL (safe working load) wire rope hoists located on monorail beams arranged at 90deg to the rotor bearing journal stub shafts.
Kicking off the scope of work and working closely with a long standing trusted subcontractor, Hoist & Winch set about designing two 41t SWL rotor lifting lugs. As the basis for this task, the company used the customer’s drawing of the 600mm diameter rotor stub shaft profile and site photographs of the original lifting lugs. Other assignments here included accurate surveys of the existing hoist runway beam centres and the hoist unit hook profile. Hoist & Winch then produced general assembly drawings for a final dimensional check on site and customer approval of the design concept.
As well as manufacturing the rotor lifting lugs, the Hoist & Winch scope included design and manufacture of a special mandrel that would allow proof load testing of the lifting lugs prior to delivery to site. Each 41T SWL rotor lifting lug had to undergo a test rig mounted, 200% static proof load test. Hoist & Winch also performed non-destructive testing (NDT) involving visual, X-ray and magnetic particle inspection (MPI) procedures, while dynamic load testing of the rotor lifting lugs took place at the customer’s site using the new replacement rotor as the test load in advance of the lifting operation.
After passing all testing requirements, Hoist & Winch issued a LOLER (Lifting Operations and Lifting Equipment Regulations) Thorough Examination Report and Proof Load Test Certificate for the new rotor lifting lugs, along with 3.1b Material Certification for all materials used.
To see the project to its conclusion, Hoist & Winch witnessed the customer’s use of the rotor lugs during a planned plant shutdown for the lifting operation to take place. In so doing, the company also provided standby breakdown cover for the pair of tandem-controlled 41t SWL wire rope hoists.
“This project demonstrates how our diverse and comprehensive portfolio of services can come to the aid of almost any lifting requirement,” says Andy Allen, director of Hoist & Winch Ltd. “Our professional team has decades of experience in lifting equipment services, for all applications. If your plant has any kind of lifting demand that would benefit from the input of industry experts, our team can help, beginning with a no-obligation discussion about the task in hand.”