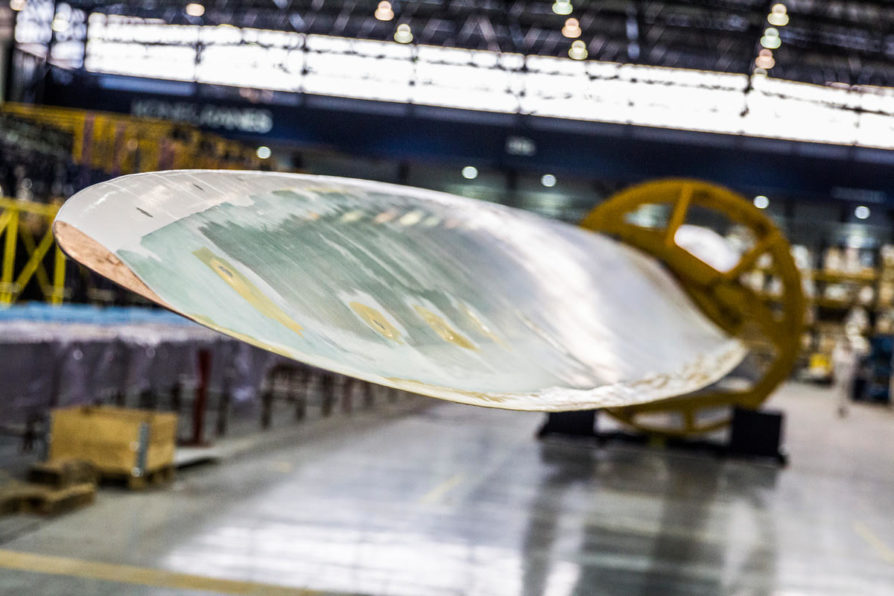)
DLM weighs turbine blades at MHI Vestas
Dynamic Load Monitoring (UK) Ltd. (DLM), of Southampton, UK has provided a wireless weighing solution for MHI Vestas Offshore Wind’s facility at nearby Fawley.
MHI Vestas needed an accurate way of measuring the weight of their 80m long turbine blades (the length of nine London buses back-to-back) at both the root and the tip upon completion of the painting process. The blades are actually made on the Isle of Wight before being transported to Fawley for painting and weighing.
Accuracy is critical as, once the blades are weighed, they are classified as light, medium and heavy for use on each turbine. Once the total weight of the blade is determined, the manufacturer is able to calculate how much ballast is applied to each blade to create the sets of three to make up a turbine. One rotation of a turbine (three blades) can power a typical home for up to 29 hours.
DLM, a specialist in the design, manufacture, repair and calibration of load cells and load monitoring equipment used throughout the renewable energy supply chain, provided a 25t capacity Telemetry Tensile Link and 20t capacity S-cell Load Cell, both selected from the company’s standard range because they are highly accurate and can be added to existing rigging equipment, easily and quickly. The data is read by the operator on two separate wireless handheld displays. The load monitoring equipment is rigged beneath the hooks of the site’s overhead lifting equipment.
James Perkins, MHI Vestas site manager at the Fawley facility, says, “Accurate data capture allows us to precisely calculate the amount of ballast material needed for each blade, which is critical when blades are mounted and spinning on the offshore wind turbines. Accurate weighing allows us to reduce future O and M [operation and maintenance] costs and ensure the blades are spinning as much as possible.”
Perkins adds, “DLM’s load cells are certainly put through their paces. Their repair and calibration team are very responsive and have a very short lead time on parts and repair works, which helps us out a great deal.”
Chris Scrutton, technical manager at DLM, says, “It’s always a pleasure to see our products associated with organisations at the cutting edge of their sector. The end user’s parent companies [Mitsubishi Heavy Industries and Vestas Wind Systems] are two of the global leaders in wind and energy. To hear that such an operation values our products and responsiveness is a tremendous endorsement. We look forward to playing an integral role in production of many turbine blades at this important manufacturing location.”
DLM provided a TL-2.0 in this instance. However, it has recently introduced a third generation of its Telemetry Tensile Link Load Cell, a lightweight wireless tension measuring unit that combines a high level of performance with a robust design for harsh environments. It is made from aerospace grade aluminium and offers a range up to 800m (over 2600ft) and a battery life of 700 hours. The TL-3.0 can be paired with one or up to a twelve handheld displays. Scrutton also pointed to the product’s 2.4GHz license-free frequency and remote power on/off feature.
The S-Cell load cell (SC-1.0), meanwhile, is available from 250kg to 20t capacities and offers welded covers, stainless steel construction, sealing to IP68, and high accuracy—in tension and compression. It is suitable for use on test stands, to take measurements during certification, and in vessel and tank weighing applications, in addition to retrofit in original equipment manufacturer (OEM) technologies and machinery.
Wind Up
Dynamic Load Monitoring (UK) Ltd. (DLM) is looking to further raise its profile in the wind energy sector throughout 2021. To that end, it has developed a data-logging device that provides load, angle, and acceleration data at high sample rates particularly for use in offshore renewables.
Chris Scrutton, technical manager at DLM, says, “With many existing wind turbines installed already, we are finding clients are now looking for ways to improve reliability and efficiency, which often involves measuring of real time data in the field. Our data-loggers have been used for measuring forces due to sea waves on array cables and have been used in R&D [research and development] projects in turbine fields. The next step in the development of instrumentation in offshore wind is remote access and data transfer.”
The system Scrutton refers to was developed in response to demand for a method of monitoring forces on cables and the movement they experience over time. In one recent example, the system logged the data over the course of a year and made it periodically accessible. The system comprises three dual axis shear pin load cells, two accelerometers, and a programmable logic controller (PLC). The shear pin load cells are dual axis shear pins that measure forces across two planes in the positive and negative directions.
The North Sea is an area of constant interest, but Scrutton also pointed to the Americas as a likely hotbed of long-term activity, highlighting Texas, Iowa, Oklahoma, Kansas, and California especially. In all areas, wind continues to present unique challenges to everyone in the supply chain. Scrutton says: “The location of instrumentation on a turbine array tends to be in the splash zone.”
He adds, “This is notoriously one of the harshest environments for cables and instrumentation to withstand. Due to the remote locations and especially bad weather in the North Sea over the winter months, maintenance and repairs can be challenging. Therefore, the systems need to be suitably designed and robust enough to withstand the harsh conditions for long periods. DLM has gained experience in supplying products into this harsh environment with tried and tested methods for success.”