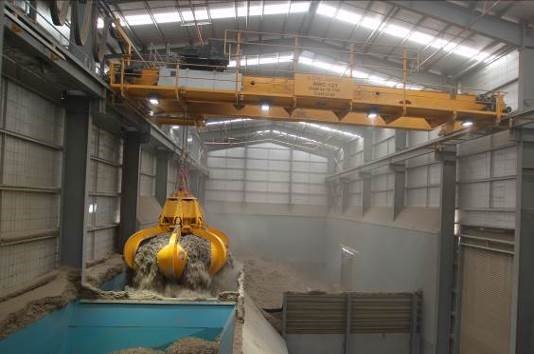)
Efficiency enhanced with 24/7 automatic handling crane
Leading building materials company, Boral Cement, is enhancing its sustainability and reducing fossil fuel dependency by using processed industrial recoverable materials as part of the fuel mix to provide heat energy to the kiln at their Berrima Cement Works.
The ‘Solid Waste-Derived Fuels’ (SWDF) project relies on a 24/7 Konecranes’ fully-automated resource recoverable materials handling crane to safely and efficiently handle processed recovered material.
David Spears, principal project manager at Solid Waste-Derived Fuels Project, Boral Cement says, “This processed recovered material is delivered by truck from Tier 1 resource recovery facilities in Sydney and the Konecranes Waste-to-Energy (WtE) handling crane moves material into hoppers that feed into a conveyor belt system that transports it to the rotary cement kiln. If the hoppers are full, the crane moves the material to a temporary storage area.”
“Important to the success of the SWDF project is having the right material handling equipment. In addition to having the right technology, the experienced service and support from Konecranes was a major factor in our decision to employ their technology,” he said.
Boral’s Berrima Cement Works – part of the nationally leading building materials organisation – employs more than 145 people and supplies more than 60% of NSW and ACT’s cement products.
A truck unloading processed recovered materials to the Solid Waste-Derived Fuels Facility, left, and the conveyor system that transports material on a 30deg angle to the kiln after the Konecranes WtE-handling crane loads the hoppers
Konecranes is the world’s largest crane service organisation, with more than 600,000 pieces of lifting equipment of all makes and models under service contract worldwide.
“Sustainability is one of our core values at Boral. The company particularly looks for initiatives that support our objective of delivering Zero Harm to employees and visitors, as well as initiatives that provide both an environmental and a cost benefit. The efficiency of the Konecranes WtE-handling crane lined up with all of these objectives,” says Spears.
The Konecranes 12t WtE-handling crane has a specialised grab attachment that can pick up 10 cubic metres of processed recovered material at a time. With the light fuel material densities at Boral’s Berrima Cement Works, it picks up approximately 4t with each full load.
“The Berrima Cement Works produces Portland Cement and the process requires measured quantities of specific materials such as limestone, shale and iron that are blended together, ground to a fine power and fused together at a very high temperature in a rotary kiln. This fused material is referred to as clinker. Previously, the main fuel used for this heating process was coal, but Boral is always striving for ways to be operationally competitive and more sustainable,” says Spears.
“The SWDF facility is designed to offset up to 30% of our annual coal usage, which makes a significant difference to the environment, and to operational efficiency.”
“Materials that would have gone to landfill are now being used as fuel, which contributes to a reduced environmental impact, and provides us with a reduction in manufacturing costs as well. It’s truly a win-win situation.”
Boral’s Berrima Cement Works is situated mid-way between Sydney and Canberra
To feed a kiln that constantly requires fuel to generate heat, Konecranes’ fully-automated WtE-handling crane operates 24/7, without needing an operator. Everything is monitored from a central control-room.
“We set ourselves demanding production targets, as we always strive to enhance our competitiveness, so an efficient and automated crane is a major benefit to our operations,” says Spears.
“There’s a natural learning curve with such an advanced crane, especially in setting up the operating parameters, layout, and engineering options. Konecranes provided us with a dedicated Industry Specialist, who was a great help. He helped us achieve the best and most efficient outcome.”
“With such a specialised crane, we are also looking to Konecranes for the ongoing service and maintenance, to ensure optimised crane lifecycle and minimal disruptions to our SWDF facility’s operations.”
With the success of the SWDF Project, Boral is already looking to the future, and examining the possibilities of further enhancing sustainability and operational objectives with resource recoverable-derived fuels.
“Our coal offset project is a major part of our Berrima Cement Works’ sustainability and we believe this project is a benefit to the community. We are already talking with Konecranes about potential further expansion, to offset even more coal in the future,” says Spears.