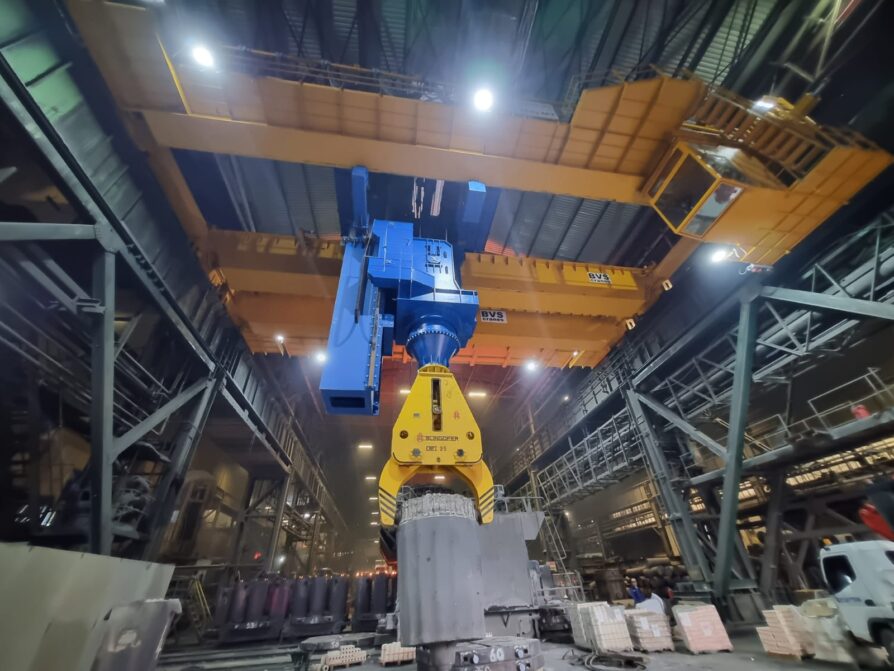)
Flawless ingot handling
The Iron age, which was an important leap in human civilization, started in 1200 BC. Despite the advances of human civilization, what we see, all around us, in the 21st Century after 2200 years is still heavily dependent on shaping iron and steel but obviously in a more advanced way.
An ingot is a piece of relatively pure material, usually metal, that is cast into a shape suitable for further processing. In steelmaking, it is the first step among semi-finished casting products. Ingots usually require a second procedure of shaping, such as cold/hot working, cutting, or milling to produce a useful final product.
Ingots also facilitate easier storage or transportation of raw materials. Steel, silver, and gold are all commonly cast into ingots for transport or manufacturing.
To create ingots, raw material of high purity is melted into a liquid state, then poured into a mould and chilled to into a hardened, useful form. Ingots may vary widely in size, weighing anywhere from several kilograms up to hundreds of tons or more depending on the material and intended purpose. Common forms for ingots include sheets, bars, and plates.
Applications of ingots
Before they can be used for manufacturing, ingots often require a secondary shaping process. As mentioned above, after they are poured into moulds either from top or bottom and stripped out of the moulds they may be cut, milled, or undergo hot/cold working processes in preparation for use in machining or other fabrication processes.
In recent years, there is an increasing in demand for large size forged steel ingots in energy and transportation industries for applications in turbine shafts, trains, ships, windmills, as raw material for making alloys, creating secondary cast, grain-free turbine blades , fabricating large steel structural components, such as I-beams , rails for railroads and so forth.
The special steels used for such applications are produced through ingot casting. However, as the size of the ingots is increasing, so does the propensity for the occurrence of quality issue in the ingots.
The handling and smooth running of the processes and flawless operation of ingot handling gains utmost importance in order to overcome any problem in quality.
High-tech ingot crane
Moving these large items can present unique lifting challenges. BVS Cranes has the capacity to custom design and manufacture lifting solutions of any size and shape to lift ingots of all sizes and configurations, which can withstand the harshest industrial environments, ranging from forges to factories. All equipment is designed and built with quality, reliability, and operator safety in mind.
Among many different applications of the larger ingot cranes, ingot stripping cranes are of critical importance in the production of quality steel. Superior steel product quality in the metallurgical sector can only be secured in facilities equipped with cranes with advanced features.
After the molten steel is poured into the moulds, the stripping and removal from the ground is carried out by ingot cranes with ‘special tong equipment’. In accordance with the production process, holding, squeezing and manipulating the material are among major duties of this crane.
Recently in the first quarter of 2023 a BVS ingot stripping crane been commissioned by one of the leading steel manufacturers operating in Western Turkey . The crane has been fully designed and built by the BVS project design department, which is a Certified R&D Centre meeting the highest criteria set by the Ministry of Industry and Technology of Turkey. Some of the new and advanced features which differentiate the BVS crane are described below by BVS business development & marketing manager, A Önder Topuz.
Technical features of the BVS ingot stripping crane
The crane has two trolleys with a capacity of 35/75t with 11m of lifting height. It is managed from an operator cabin that ensures the operator’s health, safety and comfort at the highest level.
The design has three beams with a span of 20m and a compact structure. This design created further advantages in the hook approach distances of the trolleys and the movements they make together.
Special bogie end carriage systems suitable for the three-beam structure has been designed.
The cranes has a special automation system and an advanced electrical/electronic design architecture in terms of software and hardware.
There are design features that allow ease of maintenance and labour saving such as an automatic lubrication system during the long-term use.
The crane can operate at 0-65°C and ensure daily operation of over 16 hours.