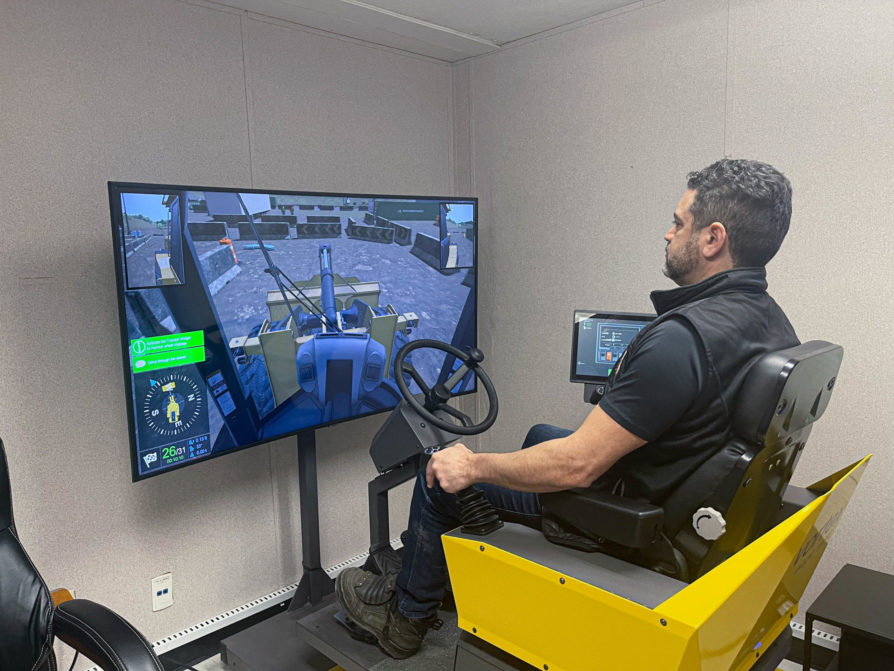)
Technology revitalises training
Gerdau Metals Recycling increases effectiveness of operator training by employing CM Labs simulators.
CM Labs Simulations, developer of Vortex training simulators, has delivered a complete suite of lifting and earthmoving simulator training programmes to Gerdau, one of the world’s largest steel producers and metals recyclers.
Gerdau recycling centres are powered by a range of earthmoving and material handling equipment. With increasing requirements for operator training, cross-training, and certification, Gerdau’s Texas-based operator training facility was looking to upgrade its programme.
Since the rollout of CM Labs simulators, Gerdau’s training programme has reduced reliance on in-field equipment by 40% and increased one-on-one trainer effectiveness by 500%.
A changing workforce poses a training challenge
Gerdau serves agricultural, automotive, construction, distribution, energy, industrial, and mining markets through its expansive network of steel production and recycling centers. The company’s Texas facility employs nearly 900 equipment operators who run forklifts, loaders, rough terrain cranes, articulated dump trucks, skid steers, and more. Because each piece of equipment has its place in the company’s daily operations, operators must be proficient on three up to nine pieces of equipment.
For most large industrial companies, equipment operator hiring, and training are ongoing processes. From new users to upskilling, cross-training, certification, and recertification of an existing workforce, Gerdau was faced with a mounting backlog of training requirements. Mobile Equipment Trainer, Jason Salmon, is tasked with managing, upgrading, and formalising the company’s equipment training programme.
Understanding that training was the foundation for success, Salmon takes this responsibility seriously. A noticeable shift in demographics added a new layer of complexity to an already difficult task.
“The workforce has changed,” says Salmon. “Just a few years ago, new hires would have at least some experience in running equipment such as a farm tractor, forklift, or something similar. But today, most of these people have little to no equipment experience whatsoever.”
For Salmon, the challenge was to not only assess, document, and advance the skill level of equipment operators at all levels, but to do so quickly and accurately, with limited resources, equipment, and budget.
A solution whose time has come
Once relegated to military, aerospace, and similar ‘hi-tech’ sectors, training simulators are making their way into construction, material handling, forestry, and power generation industries. Simulators are more effective than field training alone. Replacing remote radio-based instruction with over-the-shoulder interaction allows instructors to closely monitor activity, provide immediate feedback, and quantifiably capture progress.
Simulators help deal with the reality of labour shortage and provide a path that is easier for the next generation of operators to relate to. “We have to adopt technology to training and leverage it more fully,” said Salmon. “You can’t put an 18-year-old on a piece of million-dollar equipment and say, ‘Have at it and don’t break anything’. Simulators make equipment less intimidating and this allows new hires to feel comfortable behind the control almost immediately.”
The simulators have been a valuable tool in Gerdau’s operator benchmarking process during recruitment. They have removed any liability, risk of equipment damage, and fuel costs. They also support verification of applicant skillset claims as well as accurate placement for more experienced operator applicants.
From new employees to experienced operators, simulators offer all skill levels the power and versatility needed. From a cost and productivity perspective, simulators save on fuel consumption and reduce maintenance cycles while ensuring that productive equipment remains on the job.
However, while convinced that simulation-based training was the answer, Salmon knew that all simulators are not created equally. Salmon was looking for a simulator and technology provider to meet the following criteria:
- Closely replicate the feel and reactions of the actual equipment.
- Must be cost-effective and offer a range of equipment options.
- Provide detailed reporting capabilities
- Come with a reputation for strong and reliable customer service.
After studying the market and exploring the alternatives, it was concluded that no company matched the value and effectiveness of CM Labs.
Gerdau purchased a CM Labs Vortex Edge Max simulator for earthmoving and material handling, including telehandler, compact track loader, and crane applications along with an Instructor Operating Station for trainers to monitor and assess training sessions.
Proven results and payback
Gerdau has a thorough training policy. After receiving 12 hours of one-on-one instruction, newly hired operators are released to a supervisor for an additional 30 days of training. Today simulators are routinely used for 8 of the 12 hours needed for personal instruction. This helps to reduce the burden on instructors while saving hours of fuel consumption.
While slashing equipment dependence for new hires by as much as 40%, training effectiveness hasn’t skipped a beat. “I ran three guys through a full day on the sim. The next day they were manoeuvring a truck throughout the plant, backing it up and dumping it with hardly any instruction beyond what they learned on the simulator,” said Salmon.
Trainers can now objectively capture, track, and quantifiably measure the progress of operators in training, evaluate curriculum, and improve their effectiveness. What’s more, by physically reporting on training results for OSHA compliance and insurance documentation, simulators are making the trainer’s job more automated and organized.
Convincing upper management to invest in new technology can be a challenging sell, but Salmon says that wasn’t the case when it came to CM Labs simulators. Gerdau is putting their simulators to work in support of a continuous training process. Each week the company on-boards as many as five new hires. Add cross-training, upskilling, certifying, and recertifying of operators, along with keeping backup operators sharp, and CM Labs simulators will be running non-stop throughout the week.
“The ROI wasn’t hard to justify. From enhanced productivity to OSHA operator compliance, certification, lower fuel consumption, and reduced maintenance costs… the impact on operator productivity, safety, and our bottom line just couldn’t be ignored,” he said.