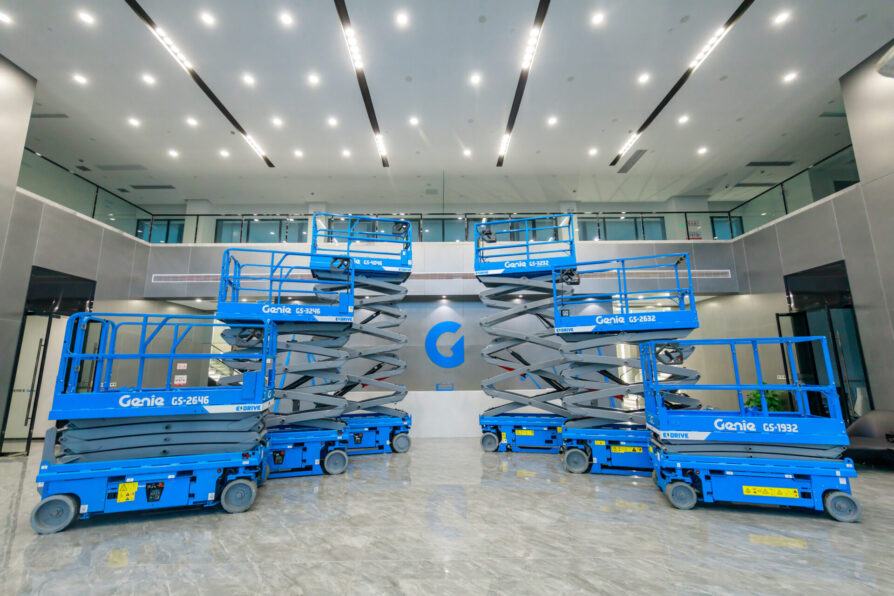)
X marks the spot
MEWP manufacturers continue to innovate in the scissor lift segment, bringing us product updates and range refreshes. Dan Jenkins finds out more.
During the late 90s and well into the 2000s, it could be argued that scissor lift development had hit a plateau. When it came to electric ‘slab’ scissors, every manufacturer had a generic range with similar performance capabilities. In many cases, the same was true of rough terrain scissor lifts. They became commodity products in rental fleets, with manufacturers seeking differentiation on areas such as price, paint finish and ease of maintenance.
The last decade saw the market become increasingly competitive as Chinese OEMs entered the fray – often with products as good as, if not better than, the major Western brands. However, competition often drives innovation, and this is certainly true of scissor lifts. Manufacturers have raised their games, bringing out new and improved products.
Unique capabilities
Snorkel manufactures a range of compact rough terrain scissors from 22ft (6.7m) to 33ft (10m). This includes two ultra-narrow models that are only 55ins (1.5m) wide, the S2255RT and S2755RT. “Currently there is not another machine in the world in the same size range,” says Andrew Fishburn, Snorkel’s vice-president of sales, UK and EMEA. “We are finding that demand is growing as more markets become aware of its unique capabilities.
“It originally did very well in Germany and is now popular in the UK, due to its narrow width and low weight. In countries where land is at a premium and commercial or residential buildings are built close together, maintenance in between structures is an issue. The contractors either erect scaffolding, with all the time and cost challenges that brings, or they use our scissor.
“The same is true for the older parts of cities, which have very narrow streets and buildings extremely close to each other – there is not a lot of room to manoeuvre. In those settings our scissors are invaluable.
“This is a real game-changer for contractors. The machine can fit on a pavement or sidewalk, and because it is under 2.8t weight it is suitable for use on concrete floors with lower load limits. In construction you will see a tower crane pick it up and position it on mezzanines and similar floors. Traditionally the option was to use a spider lift, but they have small platforms and working loads. With our scissors they can still get two people in the platform along with tools and materials.”
Rental companies can also enjoy better return on investment compared to standard RT scissors. “In the UK for example the average rental rate for a 26- or 27-foot scissor is about £120 to £130 per week. It is a very competitive market and that has only got worse due to the influx of cheaper Chinese products. However, because of its unique capabilities, our machine is averaging closer to £300 per week, so double the rate of a standard scissor lift.
“Because of this it has become a real differentiator for us and revenue generator for our rental company customers. If they can get it out three days a week at those rental rates, the return on investment is huge.
“However, rental companies must be able to communicate these unique benefits to their customers in order to achieve the higher rates. Some rental companies simply don’t have the sales culture or infrastructure to get those messages out there. A rental company will always buy on price if its sales people can only sell on price. That works to a point and manufacturers have been under pricing pressure on their scissors to meet that demand. But you can only squeeze the lemon for so long and we’ve reached a point where there is no juice left in it.”
In the EU, the forthcoming anti-dumping tariffs will change that to a certain extent. “Because of our UK manufacturing base, customers who previously did not consider Snorkel are now considering buying from us. That is partly down to some of the unique products but also about how we deal with our customers, offering attentive service.”
Across the entire RT scissor range, Snorkel offers auto-levelling outriggers. “People often underestimate the amount of time it takes to manually level outriggers,” adds Andrew. “It can take between 50 and 90 seconds to complete that process. If you are constantly moving and redeploying the outriggers, that time can really add up over the course of the day. Unfortunately, what can happen is the operator gets frustrated and either stops taking care over levelling the outriggers or even worse, stops using them altogether. Our auto-levelling avoids that risk as it is one push of a button and only takes around 11 seconds.”
Snorkel also does something different with the outrigger jack design. “Most manufacturers have it configured so that the piston rod goes down into the ground,” says Andrew. “It picks up dirt, which gets compacted and ultimately gets into the seal pack, which leads to down time for the machine. We inverted our cylinders, so a steel tube goes up and down instead, and the rod remains protected. It also eliminates risk of cylinder damage.
“All of these details and unique features add up into a compelling package. But it comes down to the rental company’s capability to sell those features to its customer base to get the higher rental rates.”
Genie’s new range
Slab scissors are also undergoing a transformation right now. The latest additions are Genie’s Next-Generation GS series, launched in mid-November. This range includes new versions of the GS-1932, GS-2632, GS-3232, GS-2646, GS-3246, and GS-4046 models.
“Genie’s next-generation design is redefining the standard for slab scissors,” says Christian Dube, senior global product manager. “From an all-new curved link stack design to a modernized look and feel, the new Genie scissor lifts are moving this classic MEWP category into the future.”
Genie’s new slab scissor lifts offer a number of unique features to benefit equipment owners and end users. “In this redesign, Genie kept the base, core E-Drive electrical components and controls—known for low total cost of ownership (TCO) and reliability—and combined it with an improved structure that is designed for quality and an even lower TCO for equipment owners and operators,” adds Christian.
“I’ll talk about the next-generation GS-1932 scissor lift, which is lighter than any other standard-sized 19 ft/6 m scissor lift, to help illustrate what I mean. For equipment owners, an integrated ladder reduces the need for ladder replacement, while operators will appreciate a 20% larger platform. Standard, fixed guardrails allow operators to pass through doorways without having to lower the guardrails, which improves efficiency. This feature also reduces wear and tear and reduces maintenance costs.
“Additionally, across the product line, components are right-sized to reduce parts replacement costs without sacrificing performance. The ergonomically designed controller in the next-generation Genie scissor lifts weighs significantly less than previous controllers, which is a feature we think operators will appreciate. Additionally, the curved link stack improves rigidity at height and aids in a smooth lift and lower functionality.”
Other additions
Genie is the latest OEM to invest in slab scissor product development. This summer, JLG launched the ES4046 electric scissor lift in Europe. “This is the latest addition to JLG’s ES slab scissor range and has both indoor and outdoor capabilities that maximise productivity,” says Nicola Sacchet, EMEAI product manager for boom, scissor and vertical products.
It is the highest scissor in JLG’s ES series, with an indoor platform height of 11.9m, reduced to 8.75m outdoors.
Features and benefits include a 350 kg/three-person capacity in indoor mode, the highest occupancy of any model in the ES series. It also has a 50% faster drive speed in stowed mode – and a 40% increase in duty cycles – compared to the R4045 scissor it replaces. It is 11% lighter than the R4045, which JLG says makes it the lightest machine in its class.
Meanwhile, Skyjack is preparing for the expansion of its E-Drive scissors for the European, Australian and New Zealand markets. This follows the successful launch of these AC brushless electric drive scissors in North America last year. The new models feature a designation carrying ‘E’ to signify E-Drive, for example, SJ3219 E.
“The simply electric range is designed to give users more, with improved efficiency, controllability, and torque,” says Malcolm Early, VP Marketing for Skyjack.
“Skyjack’s E-Drive range provides users with more; more runtime per charge, more profit from lower maintenance costs, more resale value, and more return on investment. E-Drive models boast exceptional manoeuvrability, while Skyjack’s unique scissor stack design makes these scissor lifts an ideal choice for a wide range of indoor and outdoor construction, maintenance, and industrial applications.”
Key features include an improvement of up to 20% in runtime per charge, plus more than 25% gradeability, so that climbing loading ramps is easy. In addition, the new range will carry Skyjack’s ECO mark as rental companies and major contractors face increasing demands for sustainability information. E-Drive scissors’ ECO benefits include up to 16% operational carbo savings compared to previous models.
California-based MEC AWP recently released the Micro 2032. “The machine is the size of a traditional 19-footer but has a 60% increase in capacity for trades such as drywallers,” says Gary Crook, VP of engineering. “The Micro 2032 was designed to address the many problems customers face with platform capacity limitations.”
The machine has 800lbs two-person capacity for plenty of material, fixed guardrails under 79in tall for immediate hassle-free single door transition. Twin sheet material trays on either side of the platform as standard equipment.
“Unless you have been under a rock for the last six years you will know that MEC invented the Micro class,” adds Gary. “Some competitors might have you believe that Micros are new, but they were in fact started by MEC some six years ago. This started with the Micro 19 in 2018 then expanded into the Micro 26, the Micro 13 and now the Micro 2032.”
In addition, Chinese manufacturer Sinoboom unveiled a new 19ft slab scissor at this year’s ARA show. The 1932ME ALL, sold outside North America as the 0608ME ALL is all-electric and free of hydraulic oil, presenting zero risk of leaks on jobsites.
The scissor features electric rather than hydraulic cylinders, meaning it consumes less energy, helping to drive up the run time. It comes with AGM maintenance-free batteries and an AC brushless drive motor as standard, and components are common with other electric drive scissors in the Sinoboom range.
Power strategies
This is part of a power train and battery strategy seen across several OEMs. “Electric drive scissors are more suitable for places with high environmental requirements, and which may be sensitive to oil leakage,” says Jane He, product manager at Sinoboom. “For places with wet, humid or generally harsher conditions, hydraulic drive scissor lifts are a better choice.
“Our standard batteries in slab scissors are AGM maintenance-free batteries, which help to enhance the reliability of equipment, and reduce pain-points for fleet owners and end users thanks to lower maintenance requirements and costs.”
MEC adopted AGM batteries in 2016. “AGM has been the strategy these last 8 years, and it has proven itself in practice to have been the right one,” says Gary. “AGM have proven themselves to reduce the total cost of ownership in many machine models. AGM are sealed and maintenance free and the single most predictive feature to improve ROI. Lithium batteries continue to move to being competitive but, with real world evidence that AGM batteries meet a six-year life, the balance of performance versus value currently points to AGM batteries.”
At the same time, MEC switched to direct electric drive. “It has been MEC’s strategy for some eight years now to have direct electric drive on all slab products,” adds Gary. “This is not only significantly more energy efficient which feeds directly into longer duty cycles but also indirectly improves battery service life.
“Direct electric drive also removes numerous potential leak points versus a hydraulic drive machine which inherently makes leak prevention so much easier to achieve.”
Genie takes the credit for the industry switching to electric drive. “When Genie launched its E-Drive system in 2020, it really started a trend of manufacturers moving away from other systems to AC drive,” says Christian. “Now, AC drive motors are the gold standard for the industry.
Genie E-Drive is standard on the company’s new next-generation scissors. “E-Drive helps equipment owners manage their total costs by increasing runtime per charge and reducing battery maintenance costs,” he adds. “The added bonus is that electric drive has fewer hydraulic hoses and fittings than other types of drive systems.”
When it comes to batteries, the offering still varies from region to region. “In response to customer preferences, Genie is aligning our battery strategy with local markets in terms of battery type and brand. In North America, for example, the preference is for flooded lead acid (FLA) batteries, while the rest of the world prefers AGM batteries. For that reason, Genie’s next generation slab scissor come standard with FLA batteries in North America and AGM batteries in the rest of the world. But customers also have the option to swap out the battery for a different type.
“Across the globe, Lithium-Ion is available as an option on the new GS slab scissor lifts. Genie has been focused on designing Lithium-Ion batteries for safety, quality, and the unique applications and use cases our machines experience. Adoption for this technology has been varied by region and customer strategy. Our focus here has been to design the machine for electrification by increasing the efficiency of the machine to provide the best value proposition possible. For example, by designing the machine for a lighter weight with right-sized components, the machine can more efficiently and effectively deliver the needed jobsite performance and runtime while also reducing replacement cost of components over the life of the machine.”
Genie introduced Lithium-Ion on its slab scissor lifts in 2022 after extensive testing. Genie GS E-Drive Lithium-Ion scissor lifts can be recharged in four hours and partial charges won’t damage the battery. “This allows operators to charge a lift during breaks or over lunch in the event the machine didn’t get charged the night before, or if it is being used for a second shift,” says Christian.
“Regardless of the type of battery, theft can be a common problem when lifting equipment is left unattended overnight. For this reason, we’ve added a tamper-proof battery guard housing as an option on the new scissor lifts to deter would-be thieves, reducing unexpected jobsite delays for contractors and protecting owners’ investment.”
Meanwhile JLG believes that its DaVinci slab scissor raised the bar for lithium battery machines. “The AE1932 DaVinci all-electric, zero-emission, scissor lift set a new industry benchmark as it is almost maintenance-free,” says Nicola. “The class-leading single lithium-ion battery lasts the life of the machine, and it can be charged in five minutes for 30 metres of drive, plus enough torque for loading.”
As with other OEMs, JLG’s preference going forward is for electric drive over hydraulics, while it adopts a blended approach to batteries. “Electric drive is JLG’s preferred solution because of its enhanced efficiency, which improves autonomy, and its power-to-weight ratio,” adds Nicola.
“AGM batteries are standard today in the JLG slab scissor lift range as AGM is a proven technology. Some of the main benefits of AGM batteries are that they are maintenance-free, and they strike a good balance between reliability, performance, and cost.
“To ensure we meet the needs of all our customers, however, JLG also offers equipment equipped with flooded lead acid batteries as an option.”
Skyjack’s standard offering is the other way around, with FLA as the first choice. “The EDrive scissors come standard with Flooded Lead Acid batteries,” says Malcolm. “These were chosen for their proven lifespan, reliability and performance, as well as their low kWh cost. There is also the option to use 250 Ah Batteries and AGM Batteries should that be preferred.”
Skyjack’s EDrive scissors use AC brushless electric drive motors. “As these models continue to be launched globally, they will be replacing the existing hydraulic drive models,” adds Malcolm. “The innovative drive system is used by Skyjack as it offers a superior drive experience with exceptional duty cycles and fully proportional controls. This drive system allows the EDrive range to offer improved efficiency, controllability and torque, with up to 20% more runtime per charge when compared to previous models.”
Electric RT options
Snorkel’s narrow RT scissors are available with three power options – diesel engine, bi-energy diesel and battery, or lithium battery. “The diesel and battery versions both fit on a plant trailer so can be towed by anyone with a 4×4. This adds another dimension as it means in urban areas the rental company doesn’t have to send in a truck to deliver it – this is becoming more important due to inner cities implementing emissions controls. They are saving on cost and carbon for transport.
“We are one of the only manufacturers to offer 4WD on the lithium version, which also helps us differentiate.”
Andrew views bi-energy as a bridging technology but believes it comes at a cost. “It is a compromise because it adds weight to the machines. Some rental companies do like it for the utility, because they essentially get two machines in one. When we originally launched the lithium version there were a few customers who wanted to stick with bi-energy, but we have been winning them over.
“The lithium drive train completely transformed that machine. It is much smoother to operate and has even more torque, while noise emissions are reduced up to 70%. Because of the work we put into making the diesel version so lightweight, this translates really well to an all-electric machine. Essentially it doesn’t suck as much power out of the batteries. Other manufactures use super high-capacity batteries which take much longer to charge.
“This also means that our duty cycles are superb. In standard operations you can easily get one week of operation from a single charge, which is a massive selling point for rental companies. In even lighter duties such as some industrial applications, some of our customers are getting 14 days out of one charge. Even for heavier usage, we have seen one company use the machine from 6am to 9pm and still get three days out of one charge.
“What this means is that it counters a lot of the same arguments we have seen in the automotive industry about how lack of charging infrastructure can put people off going all-electric. Contractors can rent these scissors with confidence that the battery charge will last.”
MEC recently launched the 6092 HRT, a hybrid version of its 6092 RT that has been in production for 10 years. “We have heard that in more and more applications the 6092 RT is being used under roof and a hybrid version would have strong appeal,” says Gary. “Having the choice of working on electric power only with the choice of on-
board charging when the situation allows using the small generator engine gives the flexibility to have one machine that gives up nothing on 4WD Rough Terrain performance outdoors with the flexibility to run emission free on Indoor jobs.”
MEC uses an axle-based 4WD system which it says provides the efficiency for long battery duty cycles and industry leading RT performance from the electric drive.
Sinoboom also offers electric RT scissors. “We already have a selection of 4 electric rough terrain scissor lifts, each of which correspond to a diesel version,” says Jane. “Our recently introduced range extender for the 1323RE and 1623RE models helps to significantly prolong the working time of equipment when out on jobsites where charging facilities may be in short supply. Depending on the usage scenario, up to 20 days’ extra working time can be achieved on a full charge.”
JLG offers the ERT series of electric rough terrain scissor lifts, which includes four models: ERT2669, ERT3369, ERT4069 and ERT4769. They offer working heights ranging from 10m to 16.30m. Features include a maintenance-free 2WD AC drive system and an LCD platform control box with LiftSense technology and USB charging.
“Each model offers drive capability at full height and has the largest platform size in its class,” says Nicola.
Available in Australia and EAME, Skyjack offers the SJ6832 RTE in this category. “The SJ6832 RTE offers the ability to operate indoor and outdoor with zero emissions means this compact DC rough terrain scissor lift can be the first machine on-site and the last off, to maximise utilization,” says Malcolm.
It features a 16HP brushless AC electric motor, but the majority of the hydraulic and electrical system is common with its diesel counterpart, making it easy to service and maintain.
Extras and accessories
The right accessories can transform a scissor lift, significantly adding to its productivity benefits. “The most asked for accessory, at least in North America, is the Genie Lift Tools Access Deck,” says Christian. “We’ve focused on making the access deck swapable across our next generation 32in wide scissor lifts, and we are working to bring it to other regions.”
Leak containment also continues to be a priority for those operating scissor lifts in industrial and commercial buildings. “The Genie Lift Tools Spill Guard hydraulic oil containment system is very popular, especially in North America, and will be standard on our next-generation scissor lifts in North America,” adds Christian. “It also is offered as an option on units in the rest of the world.
“We also expect the battery theft deterrent option on next generation scissor lifts to be popular. As we’ve focused on reducing costs associated with maintaining and replacing machine components, we also saw an opportunity to reduce maintenance needs and costs by offering a solution to reduce battery theft.”
MEC launched its leak containment system (LCS) in 2019 and was awarded worldwide patents in 2022. “LCS has become the acronym specified by many jobsites and contractors who need to comply with the zero tolerance of oil leaks,” says Gary. “LCS was originally an option, but it has become so popular that MEC wrapped it into being standard on all slab machines since the beginning of 2024.”
JLG also cites its CleanGuard leak prevention as a popular choice. This features custom-fit trays to capture leaks and drips from the power unit, protecting delicate surfaces from leaks and stains.
“Using CleanGuard enhances the versatility of JLG scissor lifts,” says Nicola. “It means they can be used in places such as distribution warehouses, manufacturing facilities and other leak-sensitive sites.”
Along with leak containment, safely gaining access in tight spaces such as through ceiling tiles is also important. Skyjack offers its XStep attachment in this category, providing an additional19in or 48cm of jobsite access via a second platform mounted securely on the mid rails.
“XStep is an option that enables operators to gain additional work height in tight spaces while maximizing productivity,” says Malcolm. “The design and height of the top railing on the XStep, as well as entry and exit via the locking gate, ensures operators have the same degree of security as a conventional platform.
“Notably, the XStep can be installed by one person in 5 minutes without the need for special tools. Retrofittable to previous Skyjack DC scissor models, XStep can be conveniently moved from one scissor to another, allowing for increased fleet flexibility.”
In a similar vein, MEC offers the Xtra Deck. “Xtra Deck is a patent pending feature that
has gained incredible following due to the solution that addresses the risk of a person standing on the midrails,” says Gary. “It has proven itself to have the immediacy of use when you need an additional 20in of local platform height with regulation height guardrails on all four sides yet can stow away inside mere seconds and be out of the way when not needed.”
Xtra Deck enables the operator to use the platform controls as normal to access compact overhead spaces and get through ceiling panels. “It is integral with the platform and folds down when you need it yet stows away almost invisibly when not in use. If it were not painted yellow, you might not know it is there.”